Stepper Driver Manufacturer
As a leading manufacturer of the best stepper motor drives, we offer advanced solutions designed to meet the needs of precision and reliability. Our micro and small DC stepper motor drivers are carefully designed for optimal performance in a wide range of applications.
Additionally, we provide specialized solutions made to meet your unique requirements, such as:
- Current: 3A, 4A, 5A,etc.
- Resolutions for Microstepping: 1/4, 1/8, 1/16, 1/32, and 1/64 steps
- Special Function: Silent stepper motor driver
- Step Frequency Range: 0-500kHz
- Torque: 0.1-10Nm
Home / Stepper Motor Driver
By Stepping Mode
We supports full-step, half-step, and microstepping modes for flexible to0rque, resolution, and motion smoothness control.
Full-step Driver
- Energizes two phases at a time
- Produces 1 full step per pulse
- Offers highest torque per step
- Suitable for low-resolution applications
- Typically 200 steps/rev for a 1.8° stepper motor
Half-step Driver
- Alternates between one and two phases energized
- Produces half the step angle (e.g., 0.9°)
- 400 steps/rev for a 1.8° motor
- Used where smoother motion is needed but cost matters
Microstepping Driver
- Varies current sinusoidally in phases
- Divides steps into many microsteps (e.g., 1/16, 1/32)
- Can reach up to 51,200 steps/rev with 1/256 microstepping
- Ideal for precision applications (e.g., 3D printers, CNC)
By Control Method
We offers open-loop and closed-loop control for cost-effective or high-precision motion with feedback-based real-time correction.
Open-loop Driver
- No feedback from the motor
- Position and speed are controlled by input pulses
- Simple and cost-effective
- Common in 3D printers, basic CNCs, plotters
Closed-loop Driver (Servo Stepper)
- Uses encoder feedback for real-time position correction
- Prevents missed steps and motor stall
- Smoother, quieter operation with less vibration
- Automatically adjusts current to load needs
- Ideal for high-speed or precision applications
By Feedback Support
We supports sensorless, encoder, and advanced sensor feedback for accurate control, improved reliability, and efficient closed-loop performance.
Sensorless Driver
- No feedback device; operates in open-loop
- Relies on commanded steps only
- Lower energy efficiency under varying loads
- Common in basic CNC, 3D printers, open-loop systems
Encoder-based Driver
- Uses rotary encoder for feedback
- Enables closed-loop operation with error correction
- Detects missed steps and adjusts in real-time
- Improves torque, speed, and positional accuracy
Resolver/Advanced Sensor Driver
- Uses high-resolution sensors beyond basic encoders
- Enables full closed-loop control with high precision
- Supports smoother, quieter, and more efficient motion
- Often paired with FOC (Field-Oriented Control)
- Ideal for robotics, automation, medical devices
By Phase
The phase options for stepper motor drivers provide different levels of performance, complexity, and suitability for various applications. Please contact us!
2-Phase Stepper Motor Driver
- Uses two windings (phases), typically referred to as Phase A and Phase B.
- Alternates current through the two windings to create motion.
- Simple design and control.
- Extensively employed in many different fields, including robots and 3D printers.
3-Phase Stepper Motor Driver
- Uses three windings, often referred to as U, V, and W phases.
- Provides smoother rotation and better performance at higher speeds.
- Smoother and more efficient motion due to the additional phase.
- Better torque and less vibration.
4-Phase Stepper Motor Driver
- Uses four windings (A, B, C, D phases) with a center tap.
- Each phase is activated in sequence to move the motor step by step.
- Simpler control than bipolar motors (when used with unipolar motors).
- Common in lower torque applications.
5-Phase Stepper Motor Driver
- Uses five windings.
- Provides very smooth and precise motion.
- Extremely smooth and precise operation.
- Higher torque and better performance at higher speeds.
- Lower vibration and noise.
By Power Drive Configuration
Unipolar
- Unipolar drivers use center-tapped windings with five, six, or eight wires.
- Unipolar drivers use center taps and simple transistors for easier current control.
- Suitable for applications where simplicity and cost are more critical than high torque and efficiency.
Bipolar
- Bipolar drivers use four-wire windings without center taps for each phase.
- More complex, requiring H-bridge to reverse winding current and magnetic polarity.
- Suitable for applications requiring higher torque and efficiency.
By Voltage
Please contact us!
5v
- Perfect for uses where power economy is essential.
- Often compatible with low-voltage microcontrollers and power supplies.
- 5V stepper driver generally cheaper due to lower power requirements and simpler circuitry.
12v
- A 12v stepper motor driver offers a performance-to-power ratio that is balanced.
- Still compatible with many micro controllers and power supplies.
- Higher voltage allows for better torque and speed compared to 5V drivers.
24v
- 24V stepper motor driver offers significantly higher torque and speed.
- Higher voltage improves current control, reduces losses, boosts performance.
- Suitable for larger and more powerful stepper motors.
Applications
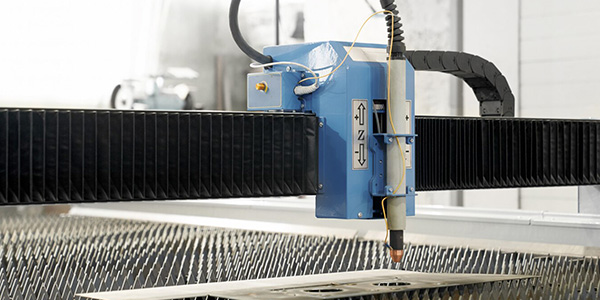
CNC Machines
- CNC stepper drivers are vital in CNC machines, ensuring precise tool movement and machine axis positioning for accurate machining.
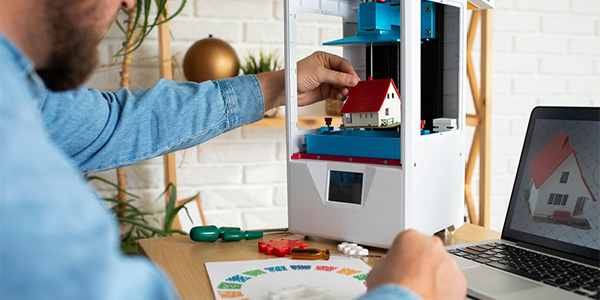
3D Printers
- In 3D printing, stepper drivers control the print head and build platform movements, ensuring precise and detailed 3D model creation.
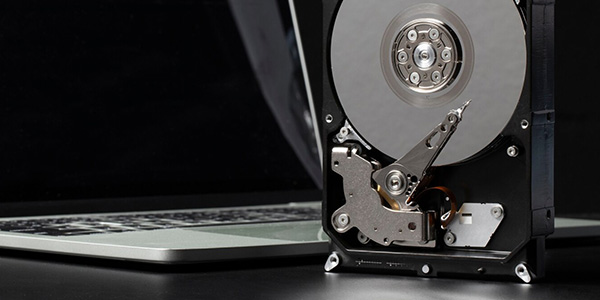
CD/DVD Drives
- Stepper motors in CD and DVD drives, also known as CD drive stepper motors, precisely move the laser assembly to read and write data tracks on discs.
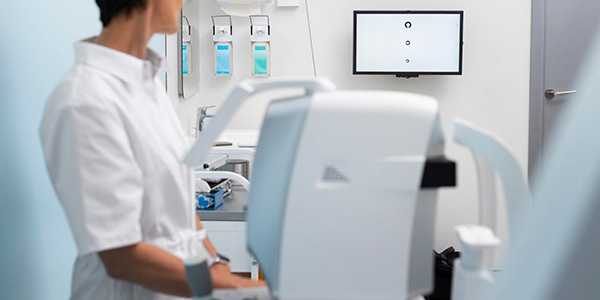
Medical Equipment
- Stepper motor drivers in medical devices ensure precise motions for imaging equipment and precision pumps.
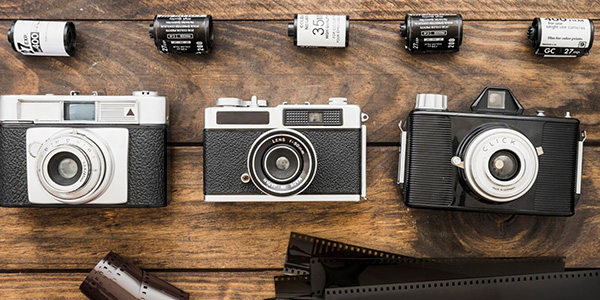
Cameras and Optical Equipment
- Stepper motors control the zoom and focus mechanisms in cameras and optical instruments. The drivers ensure smooth and precise adjustments for capturing clear images.
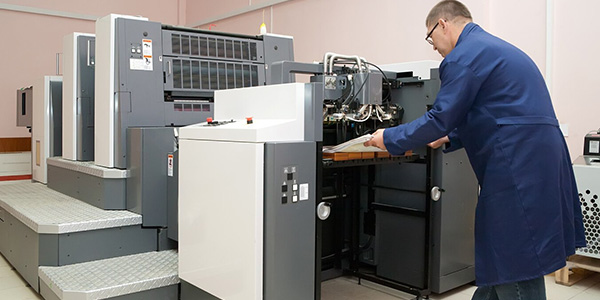
Printing Machines
- Stepper motor drivers control the movement of print heads and paper feeders in printing machines, ensuring high precision and quality in printing operations.