Linear Stepper Motor Manufacturer
We offer various models of linear stepper motors and provide precise, repeatable linear motion with high accuracy, low maintenance, and simple control, ideal for automation, medical devices, and precision positioning applications.
We can also customize product parameters for you:
- Length: 30 mm to 300 mm
- Width: 15 mm to 80 mm
- Step Angle: 0.9° to 1.8° per step
- Holding Force: 5 N to 200 N
- Travel Speed: Up to 100 mm/s to 500 mm/s
Home / Linear Stepper Motor
Components
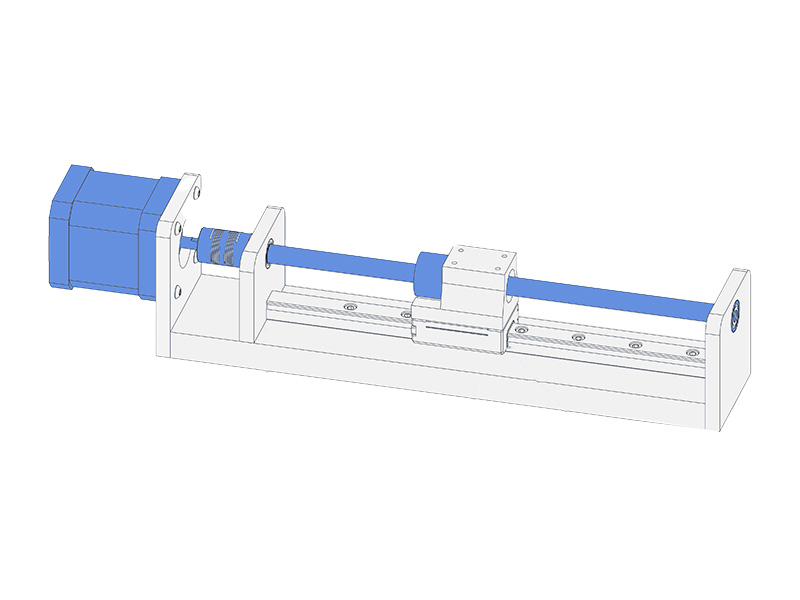
Linear stepper motor has a stator with windings, a moving rotor, and a lead screw or rail for precise linear motion.
- Stator: Contains the windings and creates the electromagnetic fields to drive the motor.
- Rotor(or Forcer): The moving element in contact with the magnetic fields of the stator.
- Lead Screw (for non-captive types): Transforms motion from rotation into linear motion.
- Linear Rail or Guide: Provides the pathway for the motor's linear motion.
- Bearings: Make certain that the lead screw or rotor moves precisely and smoothly.
- Encoder (optional): Provides feedback for precise position control.
By Construction
We can provide linear stepper motors in PM, VR, and hybrid types, offering tailored construction for torque, speed, and precision needs.
Permanent Magnet (PM) Linear Stepper Motor
- Uses permanent magnets on the moving part (forcer).
- Step angle range from ~1.8° to 7.5°.
- Smooth motion and higher torque at low speeds.
- Common in office automation, printers, and medical devices.
Variable Reluctance (VR) Linear Stepper Motor
- Has no permanent magnets, relies on reluctance variation.
- Fast response and lightweight design.
- Step angle range from ~5° to 15°.
- Used in light-duty automation tasks.
Hybrid Linear Stepper Motor
- Combines PM and VR features.
- Offers high precision, better holding torque, and smooth operation.
- Step angle range from ~0.9° to 1.8°.
- Used in medical devices, robotics, and CNC systems.
By Drive Mechanism
Our linear stepper motor offers direct and indirect-drive mechanisms for precise, compact motion control with or without mechanical transmission elements.
Direct-Drive
- Linear motion generated directly by the motor.
- No mechanical transmission elements like screws or belts.
- High precision and fast response.
- Lower mechanical complexity, less backlash.
- Ideal for clean, compact, high-accuracy systems (e.g. semiconductor, lab automation).
Indirect-Drive (Lead Screw/Belt Drive)
- Non-captive linear stepper motor features flexibility and longer stroke, and can manage external guidance.
- Captive linear stepper motor features compact, ready-to-use linear actuator with limited stroke and no need for external guidance.
From 0 to N - Full Motor Solutions
By Control Method
With open-loop, closed-loop, microstepping, current, PWM, and sine wave control, our linear stepper motor can operate with accuracy, stability, and efficiency.
Open-loop Control
- No feedback; The controller assumes accurate movement.
- Simple and cost-effective.
- Suitable for light-load or non-critical positioning tasks.
Closed-loop Control
- Uses sensors (e.g., encoders) for real-time position feedback.
- Enhances precision and makes up for lost steps.
- Perfect for heavy-load or dynamic applications.
Microstepping Control
- Divides full steps into smaller micro-steps for resolution.
- Provides smoother motion and reduced vibration.
- Useful in precision systems like lab automation.
Current Control
- Adjusts current levels to limit torque and heat.
- Protects the motor and maximizes power consumption.
- Many embedded control systems use it.
PWM (Pulse Width Modulation) Control
- Modulates voltage applied to coils using high-frequency pulses.
- Enables finer torque and speed control.
- Used within many driver ICs.
Sine Wave Control
- Generates smoother current profiles.
- Used in hybrid or high-end applications.
- Reduces mechanical noise and resonance.
Applications
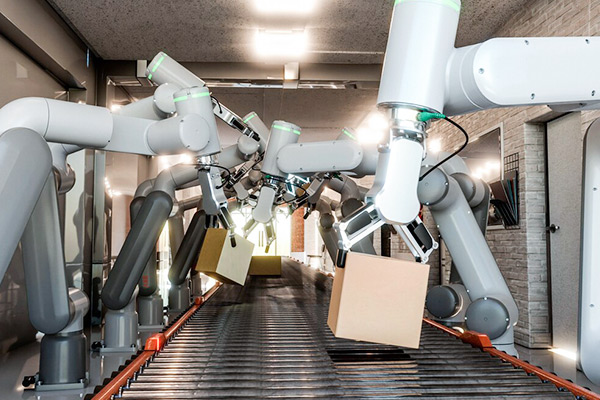
Automated Manufacturing & Robotics
- Employed in automated assembly lines to ensure accurate component placement.
- Robotics applications for accurate movement of robotic arms and grippers.
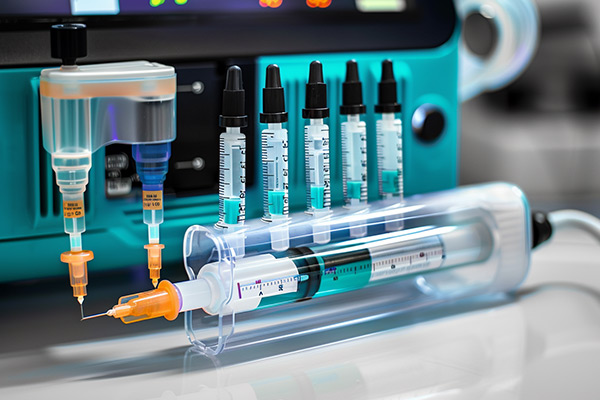
Medical & Laboratory Equipment
- Employed in medical apparatus like syringe drives and precision pumps.
- Laboratory automation for sample handling and positioning.
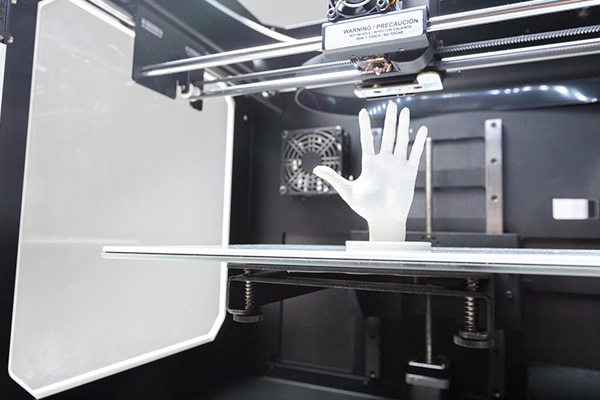
3D Printing & CNC Machines
- Essential in 3D printers for moving print heads or build platforms.
- CNC machines are utilized to regulate the motion of cutting instruments and components.
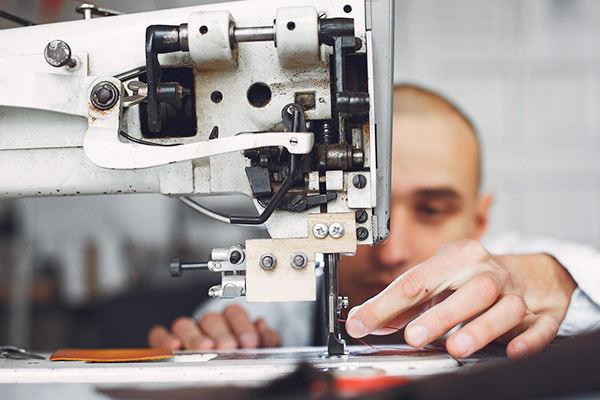
Textile & Semiconductor Industries
- Textile machinery for controlling the position of needles or fabric.
- Semiconductor manufacturing for precise handling of wafers and components.
FAQ
Do linear stepper motors require feedback for accurate positioning?
In simpler applications, they can operate in open-loop mode relying solely on step pulses. However, for enhanced accuracy and reliability, some models use encoders or linear scales for position feedback.
Which aspects need to be taken into account when choosing a linear stepper motor?
Factors include the required linear speed and acceleration, load capacity, power supply requirements, and the need for feedback control.
What considerations should be made when selecting a linear stepper motor?
Regular inspection for wear, lubrication of moving parts if applicable, and ensuring proper electrical connections are essential for maintaining optimal performance.
Can linear stepper motors be customized for specific applications?
Yes, manufacturers often offer customization options for linear stepper motors to meet specific requirements such as different shaft lengths, mounting configurations, and environmental conditions.